Behind The Scenes: Inside the Creation of a Limited-Edition Lib Tech Snowboard with Travis Rice
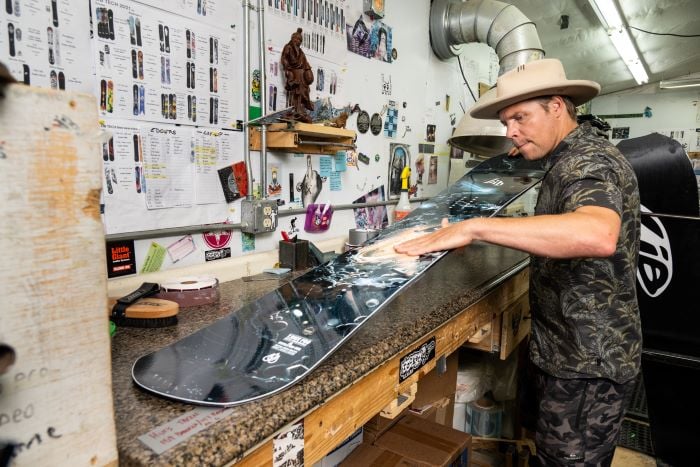
Ever wonder what goes into creating the perfect snowboard that can handle everything from park laps to deep powder lines?
Get ready to dive into the world of snowboard crafting with legendary rider Travis Rice as he builds his custom Lib Tech Travis Rice Pro snowboard at Mervin Manufacturing.
From core to camber, each board is a masterpiece in the making, designed to crush everything in its path with precision and power.
Join Travis as he crafts his next dream ride through eco-friendly, zero-waste processes that prove high-performance and sustainability can coexist.
1. Core Shop: The Heartbeat of the Board
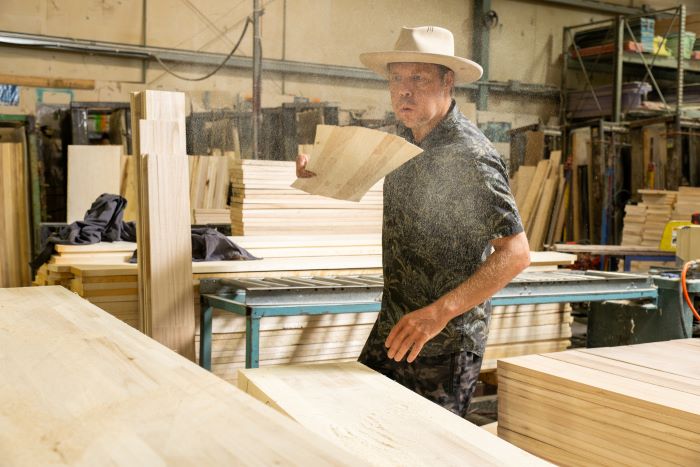
Every great ride starts at the Core Shop, where FSC-certified woods are meticulously selected and shaped for each board’s unique flex pattern.
These eco-friendly materials are layered in carefully crafted ‘recipes’ to fine-tune the board’s personality, whether it’s built for playful jibbing or charging big lines.
Even the sawdust is collected and recycled back into the environment.
2. Print Shop: Art Meets Eco-Tech
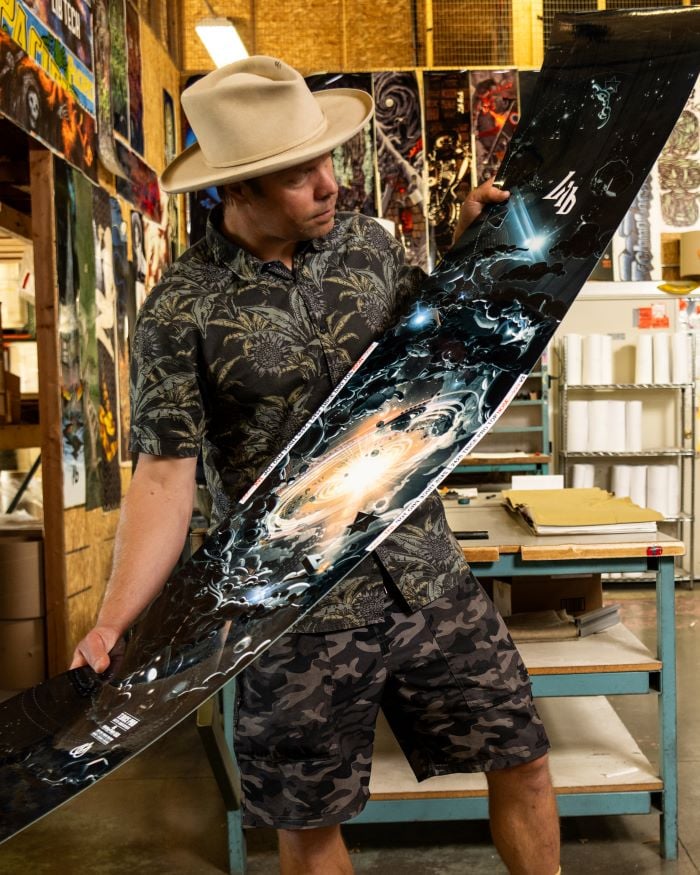
Next, it’s off to the Print Shop, where the stunning graphics that define Lib Tech’s style come to life.
Here, their proprietary eco-sublimation process transfers art to the board without any toxic silk-screen run-off—keeping harmful chemicals out of the water and delivering brilliant, true-to-life colours just as the artist envisioned.
3. Parts: Building Blocks of a Beast
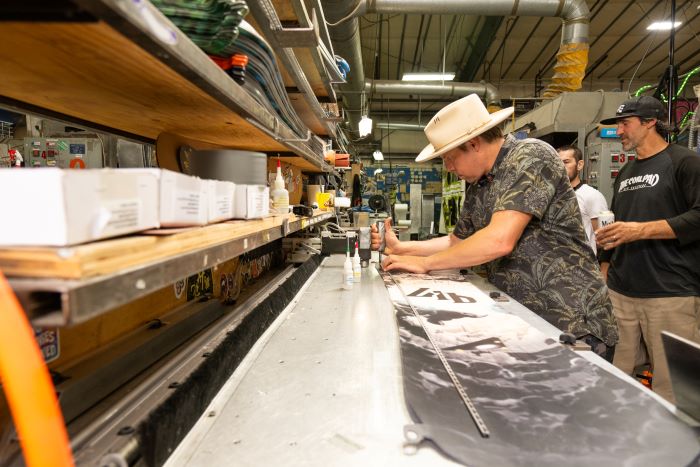
With the base, edges, tips, and tails prepped, it’s time to piece together the puzzle.
Magne-Traction edges are added for unbeatable grip, while unique tip and tail elements are shaped to match the board’s distinct feel and performance—resulting in a custom creation ready for the mountains.
4. Lay Up: Bringing it All Together
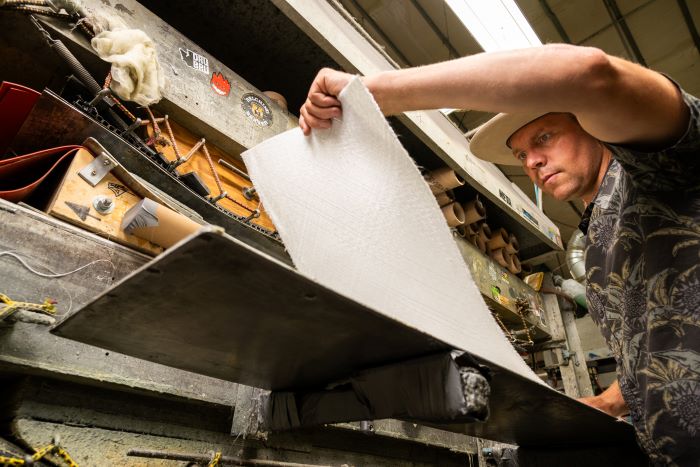
This is where the magic happens. Each piece is strategically layered with performance fibres—bi-axial, tri-axial, basalt, and carbon—then sealed with low-VOC resin to keep things environmentally friendly and odour-free.
The whole assembly is then pressed under heat and pressure, locking in the flex and power that will soon be unleashed on the slopes.
5. Finishing: Smoothing Out the Edges
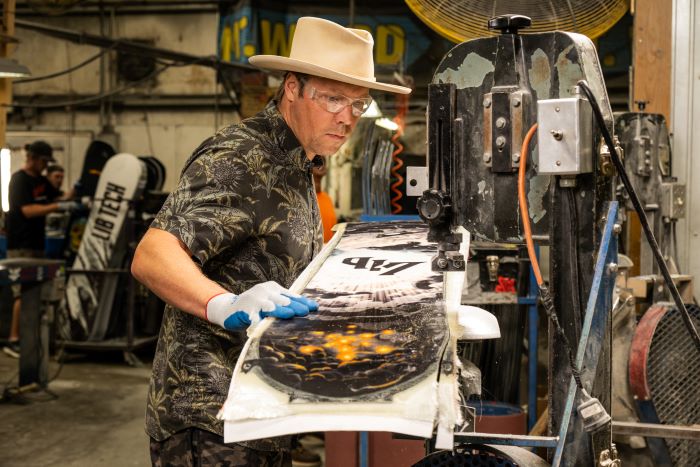
After the bake, it’s time for the Finishing crew to step in. Edges are trimmed and polished, and the board’s final shape is refined to perfection by skilled craftsmen.
The water-cleansed finishing system ensures a smooth ride and a pristine look, free from dust and impurities.
6. Quality Control: No Detail Overlooked
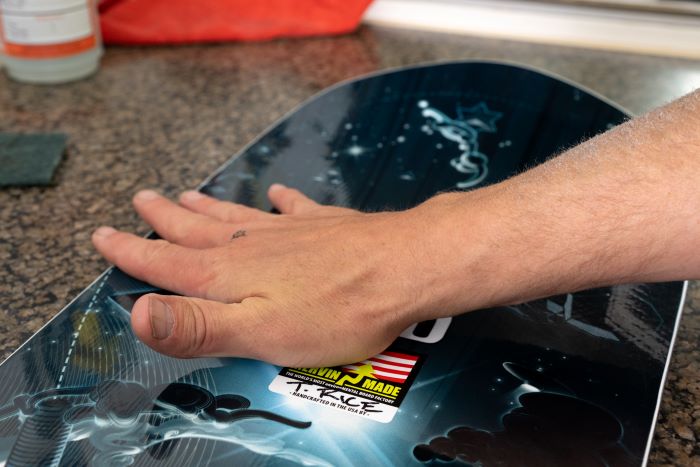
Finally, it’s over to Quality Control, where every board is scrutinised for warps, blemishes, and any imperfections.
Boards with minor flaws are marked as “B-grade beauties” and sold at a discount, while those that pass the test receive the final seal of approval from the craftsman who finished it.
7. Ready To Shred
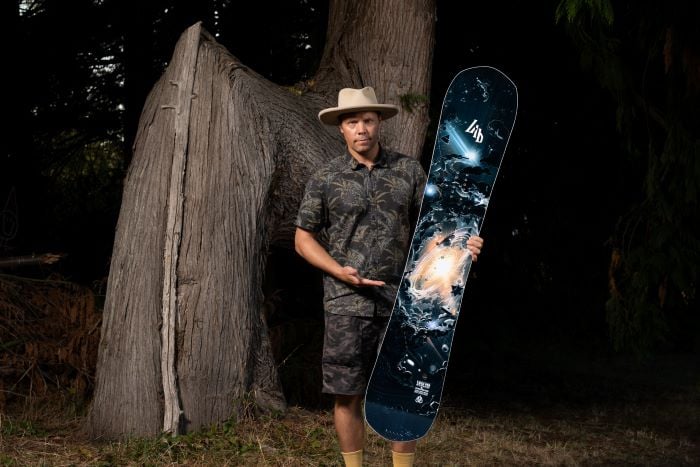
With a thumbs-up from Travis and the crew, this dream board is ready to shred.
From start to finish, each Lib Tech is more than just a snowboard—it’s a piece of riding history, handcrafted to perfection.
Loving The Factory Photos With Travis Rice? So Are We, So Here's A Few More!

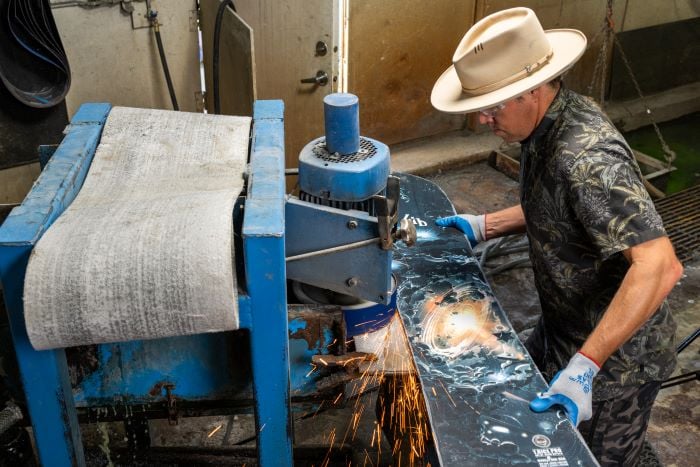
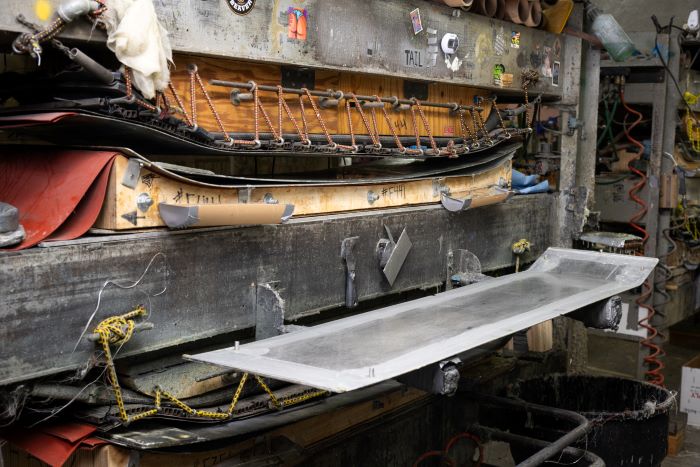
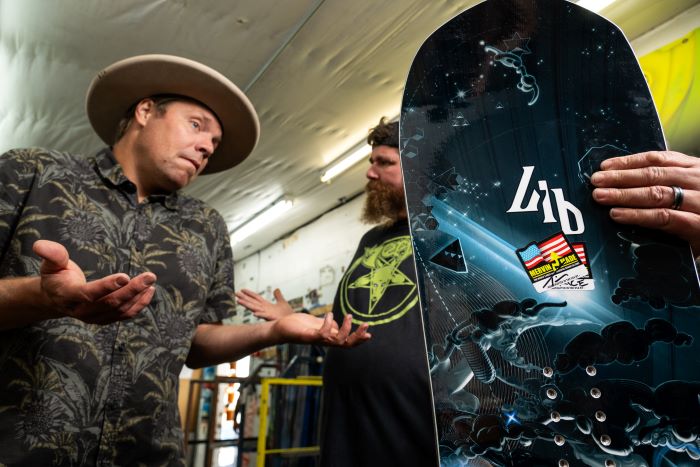
Feel Inspired? Explore All Our Latest Lib Tech Snowboards
Get Even More Stoke...
Want to get your eyes on more awesome articles like this or be the first to hear about the latest news from brands?
Check out our Snowboard Articles & Buying Guides for more long reads, technical tips and tricks, or Sign Up to our newsletter to join our community & be the first to know our latest news, stories, sales & competitions.